MANAGEMENT
By Robert (Bob) Manning, M.B.A., M.S., M.E.M., Founder, Manning Resource LLC
Recall Forensics: Uncovering the Hidden Triggers Behind the Surge in Food and Beverage Recalls—Part 2
Building resilience through attention to detail is an invaluable strategy for closing critical food safety gaps and preventing costly recalls
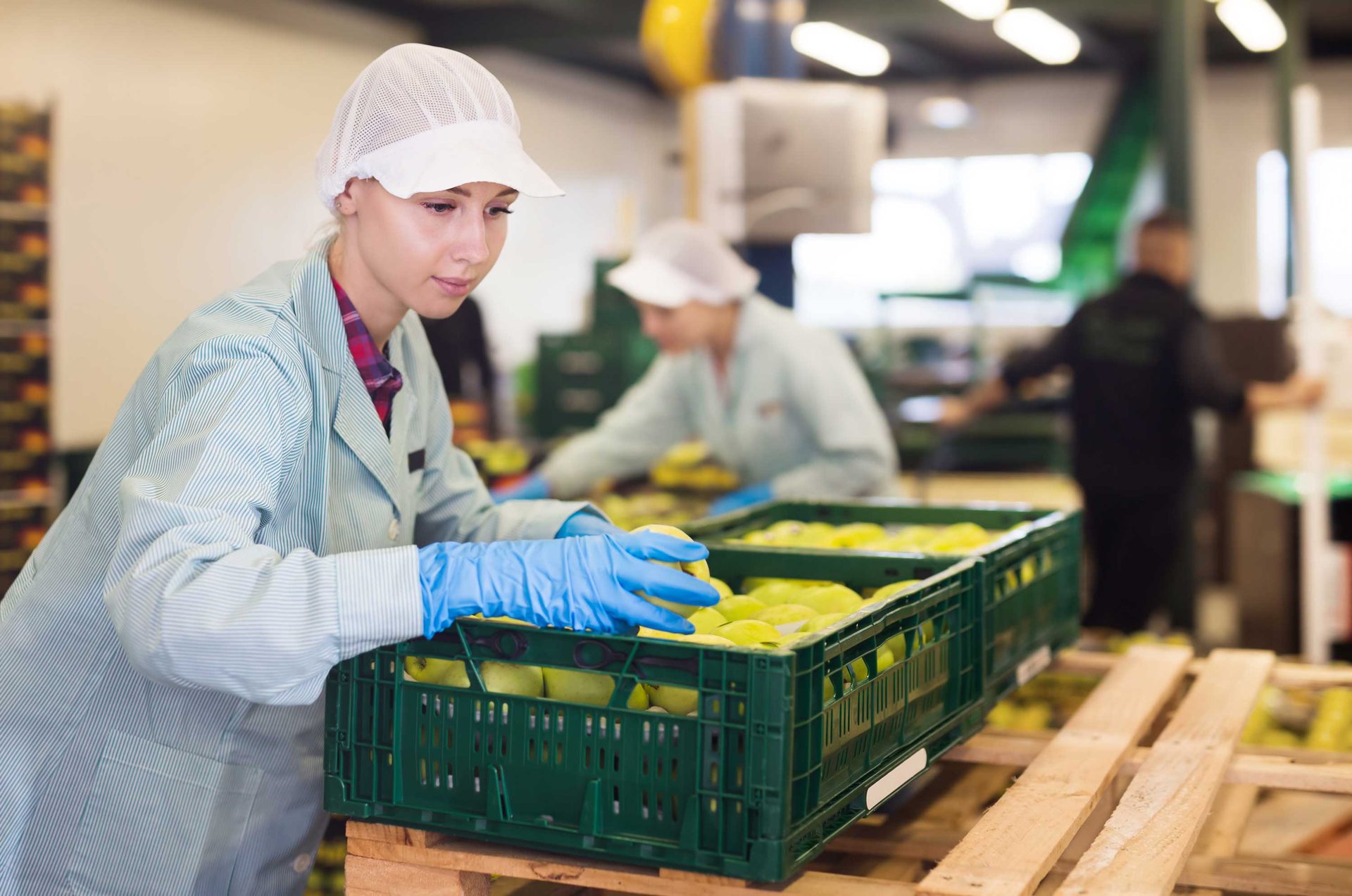
Image credit: JackF/iStock/Getty Images Plus via Getty Images
SCROLL DOWN
In Part 1 of this article series,1 we explored the foundational roles of leadership, culture, infrastructure and equipment, sanitation, and maintenance in preventing food and beverage recalls. Continuing our discussion, we focus on a new set of critical precursors: employee development, supplier relationships, ingredients and packaging, technology, and change management. These factors form the backbone of a resilient operation, influencing everything from daily processes to long-term, strategic outcomes. In this second installment, we will examine how prioritizing these areas can reduce risks, prevent costly recalls, and strengthen the overall foundation of food safety and operational excellence.
Precursor 6: Employee Development
It is often said that employees are an organization's greatest asset. This is especially true in the food and beverage industry, where operational excellence relies on a skilled, engaged, and knowledgeable workforce. However, hiring talent alone is not sufficient. Organizations must prioritize robust training and development programs that equip employees to excel. Without this commitment, gaps in skills and understanding can lead to significant risks, not just for individual employees but also for the entire company.
Unfortunately, companies often recognize the importance of employee development only after a recall or major failure, prompting reactive measures such as hiring senior training managers and deploying trainers across facilities. While these efforts can address immediate issues, they are no substitute for a proactive, ongoing commitment to training and development.
Effective employee development begins with comprehensive onboarding, but must extend far beyond initial training. Ongoing education through refresher courses, hands-on workshops, and advanced learning modules ensures that employees stay aligned with evolving best practices, emerging technologies, and regulatory updates. It is equally important that training programs assess and reinforce comprehension, empowering employees to apply their knowledge confidently in real-world scenarios.
Moreover, engaging employees in regular, meaningful conversations about their career aspirations and interests is critical to successful development strategies. This feedback helps tailor individual growth plans and feeds into the organization's succession planning model. Companies can identify subject matter experts (SMEs) and potential leaders by understanding employees' goals, creating targeted development pathways, and ensuring long-term organizational resilience. When employees see that their input is valued and that clear opportunities for advancement exist, they feel a deeper sense of belonging and purpose within the organization. This alignment between employee aspirations and organizational goals fosters stronger engagement, boosts morale, and significantly improves retention.
When organizations prioritize employee development—through robust training, continuous feedback, and thoughtful succession planning—they build a pipeline of capable, motivated talent that drives long-term success. This approach reduces risks, enhances operational resilience, and positions the company as an employer of choice, fostering a culture where employees feel valued, empowered, and ready to contribute to organizational excellence.
Precursor 7: Supplier Selection and Relationships
Supplier selection and relationships play a pivotal role in determining whether a company consistently produces high-quality products or exposes itself to costly risks, including recalls. Selecting suppliers based solely on price—without thoroughly evaluating their history, sourcing practices, quality standards, and compliance with regulations—significantly increases a company's vulnerability. A short-term cost-saving approach often overlooks the long-term value of reliable suppliers who prioritize quality, food safety, and ethical practices.
Equally important is the nature of the relationship between the company and its suppliers. Treating suppliers as transactional entities or fostering adversarial relationships limits opportunities for collaboration and innovation. Conversely, developing strong, trust-based partnerships can improve product quality, streamline operations, and even co-create innovative solutions. Suppliers who feel valued are more likely to engage proactively in solving challenges and delivering consistent results, benefiting both parties.
Supplier relationships are particularly critical in managing the complexities of recalls and preventing potential failures before they occur. Effective partnerships enable companies to establish clear expectations, conduct thorough audits, and ensure food safety and quality standards alignment throughout the supply chain. These strong relationships also foster effective communication and collaboration, allowing suppliers and organizations to work together to address potential risks and identify opportunities for improvement. This aspect is especially relevant when considering earlier discussions on ingredients and packaging, as supplier inputs have direct impact on a product's operational performance, integrity, compliance, and overall quality.
Ultimately, investing in supplier selection and relationships is about mitigating risks and creating a resilient, collaborative supply chain. Organizations can transform supplier interactions into strategic advantages by prioritizing transparency, shared goals, and open communication. This approach enhances operational performance, reinforces food safety, and drives sustainable success in an increasingly competitive marketplace.
“Technology can be a powerful tool, but without a clear strategy and robust implementation plan, it can introduce as many risks as it mitigates.”

Precursor 8: Ingredients, Packaging, and Components
Ingredients, packaging, and even cleaning chemicals are critical components that, if not appropriately managed, can result in costly recalls. When a new product is being developed or introduced into a company, the initial focus is typically on using high-quality ingredients and packaging to showcase the product's best potential. This ensures that the product can meet high consumer expectations and make a strong market debut. However, this is not always the case. In some instances, compromises in quality occur during development, leading to delays, extended testing periods, or even decisions to halt the project or upgrade failing components to meet standards.
Once the product launches and gains traction in the marketplace, another set of challenges can arise. Companies may initiate cost-reduction measures as part of profit margin improvement strategies. While reducing costs is a valid business objective, these changes can sometimes bypass normal evaluation processes due to poor communication or rushed implementation. When corners are cut, even inadvertently, the consequences can be significant. At the production facility, the product may appear to meet quality standards. Still, issues may surface later during distribution, at the retail level, or—most critically—when the product reaches consumers. These failures can manifest as compromised product integrity, reduced shelf life, or food safety concerns, leading to damaged customer trust and potential recalls.
Equally important is following proper storage recommendations and adhering to shelf life requirements for ingredients, packaging, and finished products. Deviating from these guidelines can have a cascading effect, leading to inefficient operations, increased waste, or worse, costly food safety and quality failures. Ingredients and packaging stored in suboptimal conditions may degrade, compromising functionality or food safety. Similarly, extending the use of components or products beyond their intended shelf life increases the risk of contamination, product failure, or regulatory noncompliance. Ensuring that all components are handled, stored, and used according to established guidelines is fundamental to maintaining product integrity and preventing avoidable failures.
Proper ingredient and packaging management requires strict adherence to evaluation protocols at every stage of the product lifecycle, from development to post-launch modifications. Cross-functional teams, including product development, quality assurance, procurement, and supply chain management, must be involved to ensure that any changes to components are thoroughly vetted. Additionally, supplier relationships must be leveraged to maintain transparency and collaboration, ensuring that cost-saving measures do not come at the expense of quality or safety.
Companies can mitigate risks associated with ingredient and packaging changes by fostering a culture of vigilance, communication, and adherence to best practices. This proactive approach protects product integrity and consumer trust and ensures that operational efficiencies are achieved without compromising food safety or quality. A strong focus on component management strengthens the foundation for long-term success in a competitive marketplace.
Precursor 9: Technology
You may wonder why technology is listed as a precursor when its primary goal in many organizations is to enhance processes with greater accuracy and efficiency. The challenge lies not in the use of technology itself, but in fully understanding its capabilities and limitations, as well as establishing the disciplines and controls necessary to ensure its effectiveness. Technology can be a powerful tool, but without a clear strategy and robust implementation plan, it can introduce as many risks as it mitigates.
Before incorporating technology into operations, several critical factors must be evaluated. First, the objective for its use must be clearly defined—what specific problem is it solving, or what measurable improvement is it driving? Second, the costs must be carefully considered, including not just the initial investment but also long-term expenses for calibration, maintenance, updates, and eventual upgrades. Employee training and development are equally important, as even the most advanced systems can fail without a knowledgeable workforce to operate, maintain, and troubleshoot them effectively.
Another key consideration is contingency planning. Companies must be prepared for technological failures and have clear protocols for managing operations when systems are non-functional. For example, if a critical piece of equipment fails and cannot be used for several days, how will production schedules be adjusted, and what impact will this have on product quality, delivery timelines, and customer satisfaction? A well-thought-out plan ensures that business continuity is maintained even in the face of technological setbacks.
Finally, technology should never be seen as a catch-all solution or a substitute for operational discipline. The same rigor, attention to detail, and focus on quality must be applied whether or not advanced systems are in place. Technology should enhance, not replace, strong foundational processes and practices.
When implemented strategically, technology can drive significant improvements in efficiency, accuracy, and overall performance. However, its true value is realized only when it is part of a broader strategy that includes clear objectives, disciplined execution, thorough training, and robust contingency planning. By approaching technology adoption with intention and care, organizations can maximize its benefits while minimizing potential risks.
“One of the challenges with change management is that the impact of a change may not be immediately apparent.”

Precursor 10: Change Management
Change management is a critical component of any food and beverage manufacturing program. It provides a structured approach to evaluating, implementing, and monitoring changes. A robust change management process ensures that proposed modifications are thoroughly vetted, risks are identified, and sound decisions are made. Companies expose themselves to significant risks without an effective program, including product failures, safety concerns, and recalls.
One of the challenges with change management is that the impact of a change may not be immediately apparent. Early indications of success can be misleading, as potential negative ramifications may take weeks, months, or even longer to surface—sometimes becoming evident only after products reach consumers. This underscores the importance of proactive monitoring and follow-up to assess the long-term effects of any change.
An effective change management process begins with clearly defining what should and should not be included in the program. By setting these parameters upfront, companies can ensure that the process focuses on changes that carry meaningful risk or operational significance, avoiding unnecessary administrative burdens. It is equally important to communicate the program's scope, purpose, and procedures to every level of the organization. When all teams, whether on the production floor, in quality assurance, or within leadership—are aligned and informed, the program becomes more effective and ingrained in the company culture.
A successful change management program also relies on the collaboration of a cross-functional team that brings together expertise from operations, quality, food safety, and other relevant departments. This team works to identify risks, develop mitigation strategies, and establish monitoring programs to detect and address any issues early in the process. Clear documentation and consistent communication are essential to ensuring that all stakeholders understand the scope of change, rationale, and anticipated outcomes.
The risks for companies needing a formal change management program are too significant to ignore. Immediate steps should be taken to create and implement a simple yet effective process. This includes defining roles and responsibilities, establishing clear protocols for evaluating and approving changes, and building ongoing oversight and assessment mechanisms.
A well-designed change management program reduces risks and fosters a culture of accountability, collaboration, and continuous improvement. By embedding this process into their operations—and ensuring that its purpose and procedures are understood company-wide—businesses can confidently navigate changes while protecting product quality, consumer trust, and overall company performance.
Takeaway
The food and beverage industry operates in a high-stakes environment where the smallest oversight can lead to significant risks, including product failures, recalls, and loss of consumer trust. Companies can build a robust framework that mitigates these risks by identifying and addressing key precursors such as leadership, culture, infrastructure, sanitation, maintenance, employee development, supplier relationships, ingredients and packaging, technology, and change management. Each precursor represents a vital component of operational resilience, requiring thoughtful strategies, proactive planning, and a commitment to continuous improvement.
Leadership sets the tone, culture fosters accountability, and structured processes like change management ensure consistency and adaptability. Investment in employee development and supplier relationships enhances collaboration and engagement, while vigilant attention to ingredients, packaging, and technology safeguards product quality and safety. Together, these elements create an ecosystem where risks are minimized, opportunities for innovation are maximized, and operational excellence becomes the standard.
By embracing a proactive, holistic approach to managing these precursors, organizations can prevent costly failures, drive sustainable growth, and build stronger brands. The ultimate goal is not just compliance with industry standards, but to exceed them to earn the trust of consumers, partners, and stakeholders alike. With a strong foundation built on these principles, companies position themselves as leaders in the industry, prepared to navigate challenges and achieve long-term success.
References
- Manning, Robert. "Uncovering the Hidden Triggers Behind the Surge in Food and Beverage Recalls—Part 1." Food Safety Magazine December 2024/January 2025. https://www.food-safety.com/articles/9993-uncovering-the-hidden-triggers-behind-the-surge-in-food-and-beverage-recallspart-1.
Robert (Bob) Manning, M.B.A., M.S., M.E.M., has worked in the food and beverage industry for over 30 years in various facility and senior corporate positions. He is Founder and Principal Consultant at Manning Resource LLC, and previously worked as Vice President of Technical Operations at Niagara Bottling. He has spent most of his time in operations and quality roles for large companies such as HP Hood LLC, Campbell's Soup, and Niagara Bottling, as well as consulting for major domestic and international firms. He is also the author of In the Midst of a Recall: Recall Management and Prevention Strategies in Real World Scenarios, which walks the reader through what actually happens in a major product recall. Bob holds a B.S. degree in biology from Salem State University, an M.B.A. and a master's degree in engineering management from Western New England University, a master's degree in food safety from Michigan State University, and a master's degree in strategic management and executive leadership from Pennsylvania State University.